NEWS & INSIGHTS
FROM CONCEPT TO CREATION: A BEHIND-THE-SCENES LOOK AT TROJAN’S ACRYLIC BATH MANUFACTURING PROCESS
By David Mosley, 16.04.25
At Trojan, the process of creating our acrylic baths combines traditional craftsmanship with modern manufacturing techniques. From initial concept and design through to manufacturing and the final product, each of our baths are crafted with care by our team in three distinct factories.
In this blog, we share a behind-the-scenes look at our manufacturing process, from casting through to installation, that enables us to produce precise, high-quality baths.
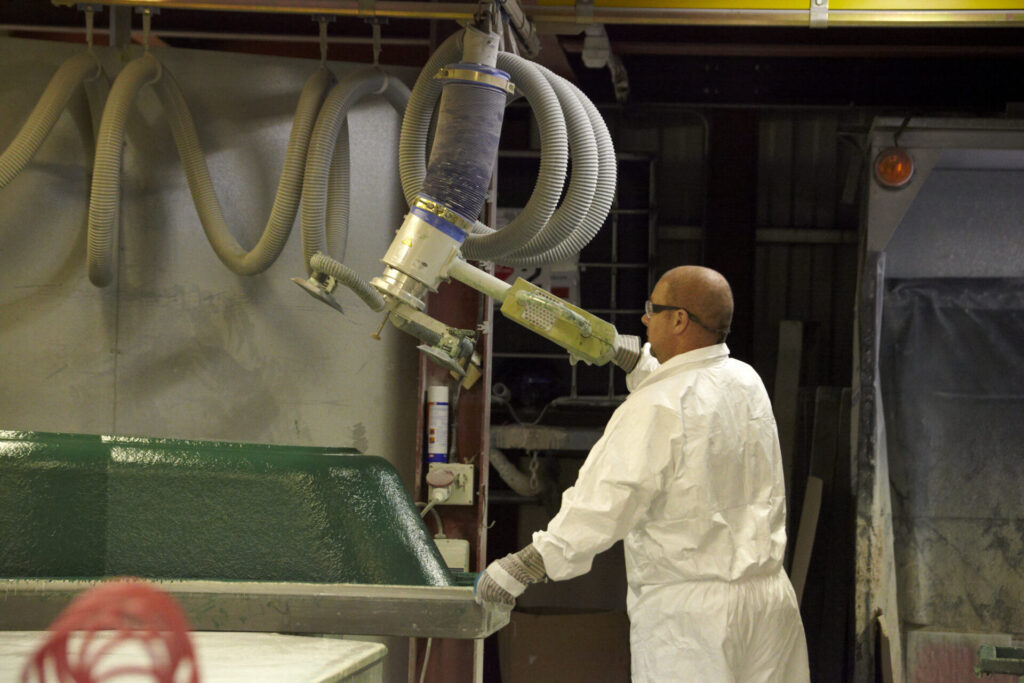
Why we use acrylic
The lightweight and durable qualities of acrylic make it perfect for manufacturing baths, with the ability to be moulded into a variety of shapes and sizes to suit different styles. Each bath begins with a premium cell cast acrylic sheet (EN263), known for its exceptional durability and luxurious finish. During polymerisation, the Methyl methacrylate (MMA) cross-links to create a material that is both UV stable and chemical resistant.
This means that our baths maintain their colour and integrity even after years of exposure to natural light and bathroom cleaning products – ensuring long-lasting performance.
Step one: Heating and moulding into shape
The manufacturing journey starts when the acrylic sheets are heated to precise temperatures, a critical step that ensures optimal flexibility without compromising the material’s integrity.
Once the perfect temperature is achieved, the sheets are vacuum formed over aluminium moulds to create a bath shell. There is a mould for each of Trojan’s bespoke bath shapes, designed for different bathing purposes and bathroom aesthetics.
Step two: Reinforcement with glass fibre polyester resin
While the bath now has its recognisable form, the process is far from complete. Each shell must be meticulously reinforced with glass fibre polyester resin.
This reinforcement process includes the careful encapsulation of a baseboard, which provides the structural integrity and stability essential for a long-lasting acrylic bath.
Step three: Controlled curing process to create a robust structure
After reinforcement, our baths undergo a carefully controlled curing process in a thermal tunnel. This crucial step ensures the complete hardening of the resin, creating a robust structure that will withstand years of use.
Once cured, the excess material – or “picture frame” – is trimmed away to reveal the clean lines of the finished bath. All offcut materials are sent to one of our two specialist on site recycling facilities, where they are processed, separated and cleaned, before being sent back to our suppliers or sold to other industries for reuse to create a closed loop supply chain. This helps us to reduce the amount of plastic waste being sent to landfill.
Step four: Custom requirements and seamless installation
Each bath can be custom drilled according to specific customer requirements. This bespoke approach ensures that every product leaves our facility to our customers specification, which will vary depending on their geographical market.
The difference with Trojan baths
At Trojan, what sets our manufacturing process apart is not just the careful attention to each step, but the proprietary techniques we’ve developed over almost 50 years of experience. While the process might seem straightforward to an observer, there are certain secrets to our method that we keep close to our chest as a bath manufacturer. These nuances are what enable us to offer our unique guarantee of 100% water drainage and 25 years of trouble-free use when correctly installed.
The combination of our thermal curing techniques and specific resin formulations creates a product that maintains its structural integrity and appearance far longer than the industry standard. And we’re proud to say that once completed, our baths meet the stringent requirements of EN 14516:2015+A1:2018 (CL.1), the European standard for domestic baths.
From sheet to showroom, every acrylic bath we create is a testament to our commitment to quality and the craftsmanship of loyal employees who care. While manufacturing techniques may evolve, our dedication to creating products that enhance our customers’ homes for decades remains unchanged.
Read more about the Trojan difference to learn what makes us stand out.